Bio-Inspired Hexapedal Robot
Gizmo - Individual
Date
January 2023 - February 2023
Location
IMPERIAL COLLEGE LONDON YEAR2
Problem: How might we develop a small conceptual robot based on the RHex architecture morphology features while optimizing its manufacturing and assembly process?
Solution: Design a chassis and mobility system for a bio-inspired mini hexapedal robot (RHex) for locomotion in rough terrain, achieving easier serviceability, lower cost, versatile movements, and simplified mechanical characteristics

The Whole Journey

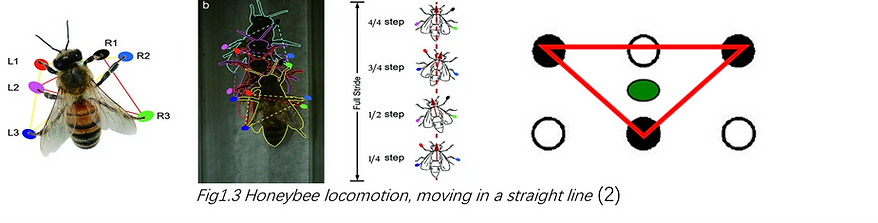

Dynamic maneuvers inspiration
To effectively perform self-autonomous tasks, it is essential to learn about biomimicry for advanced robotic motion planning. I have also deepened my understanding of cognitive processes and behavioral rules, which are crucially intertwined in real animals.
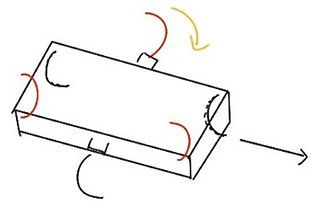

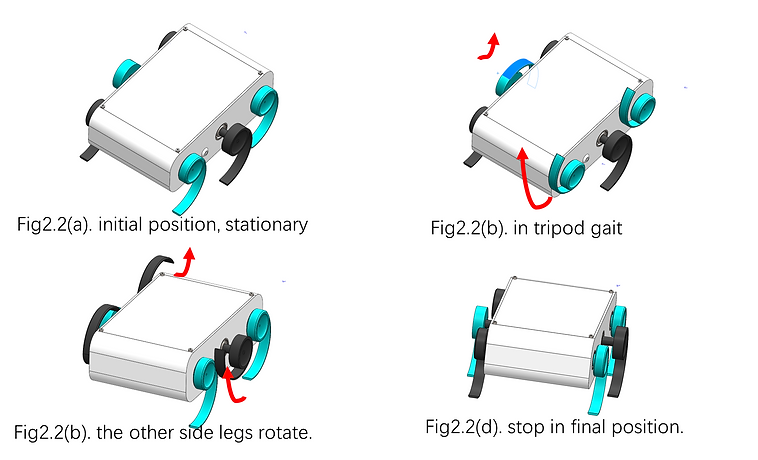
Walking Motion
The use of a diagonal tripod gait is continued to maintain whole-body stability during motion. This strategy effectively tackles the issue of interference encountered when all three legs on the same side are in motion. To enhance this solution, a timing belt mechanism has been designed and iteratively refined.


Rotating Mechanism
A bevel gear design is employed to facilitate the triangular gait in the bio-inspired robot, enabling the middle leg to move in reverse while matching the speed of the front and back legs. This design is crucial for the robot's stable and efficient maneuverability.

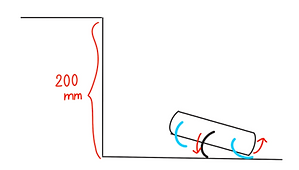



Reduction Gearbox
Design
Jumping, a motion requiring bio-inspired robots to generate high torque to overcome gravitational force and launch into the air, necessitates the determination of jumping torque. This is crucial for selecting the appropriate motor and ultimately designing a reduction gearbox

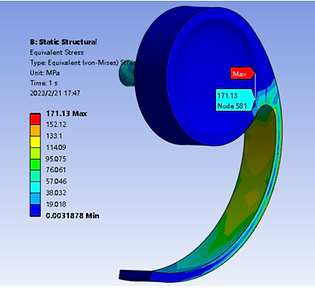
FEA Analysis
Evaluating stress and structural integrity during the robot's landing phase post-jump, carbon fiber was identified as the optimal material. Its outstanding strength-to-weight ratio was deemed most suitable for withstanding the dynamic stresses experienced during the landing motion, thus ensuring both the functionality and longevity of the robot.
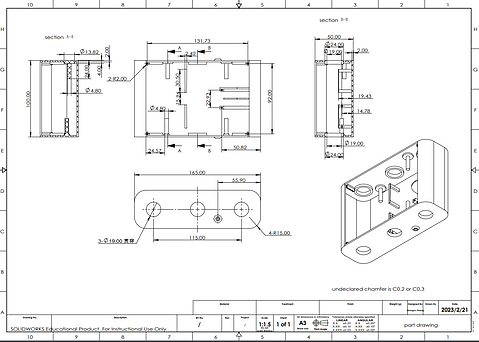

